A Master Guide to Construction Bidding
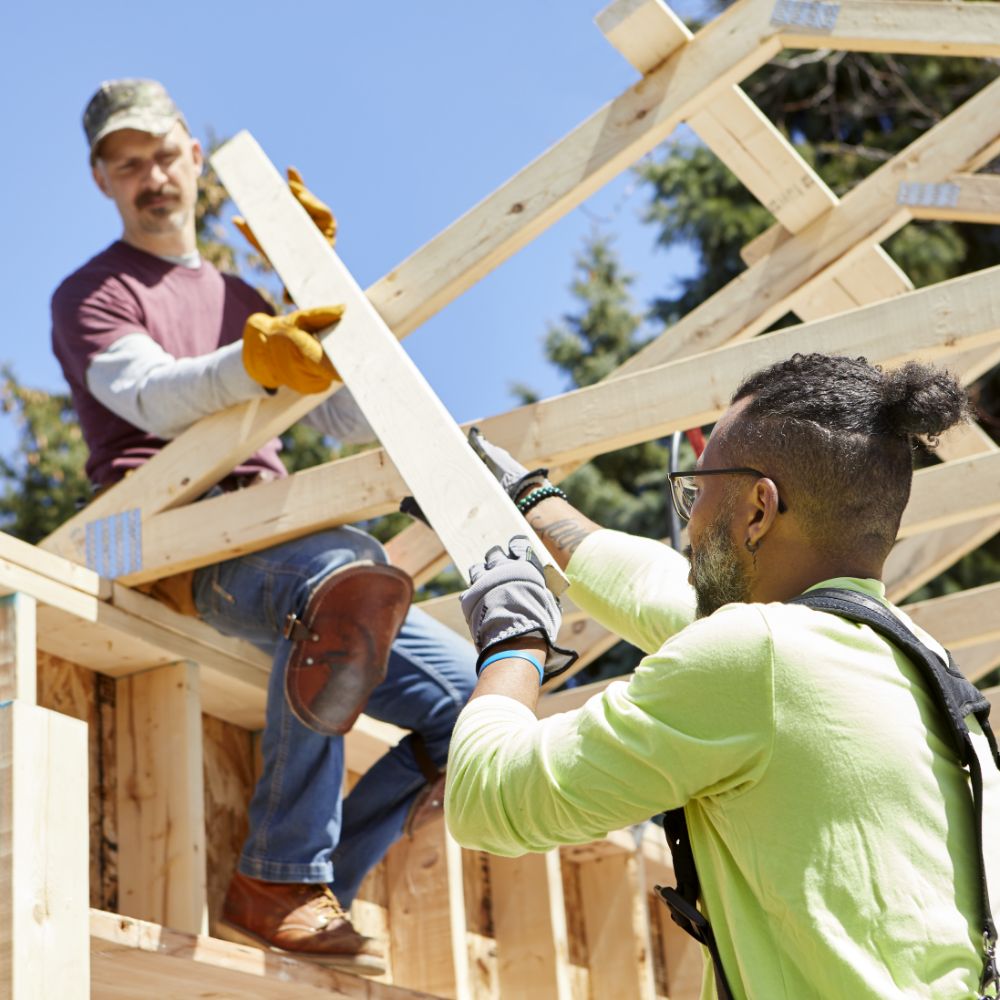
Last updated August 12, 2024
Effective construction bidding is key to securing new work in commercial, residential, industrial or government sectors. Making accurate estimates for bids is crucial to doing the work profitably.
This guide reviews the essentials of construction bidding including how to estimate labor and materials for construction jobs.
Table of Contents
What Are the Basics of Construction Bids?
How to Estimate Materials Costs
How to Estimate Labor Costs
Tips for Construction Bidding
More Tools. More Products. More Perks.
What Are the Basics of Construction Bids?
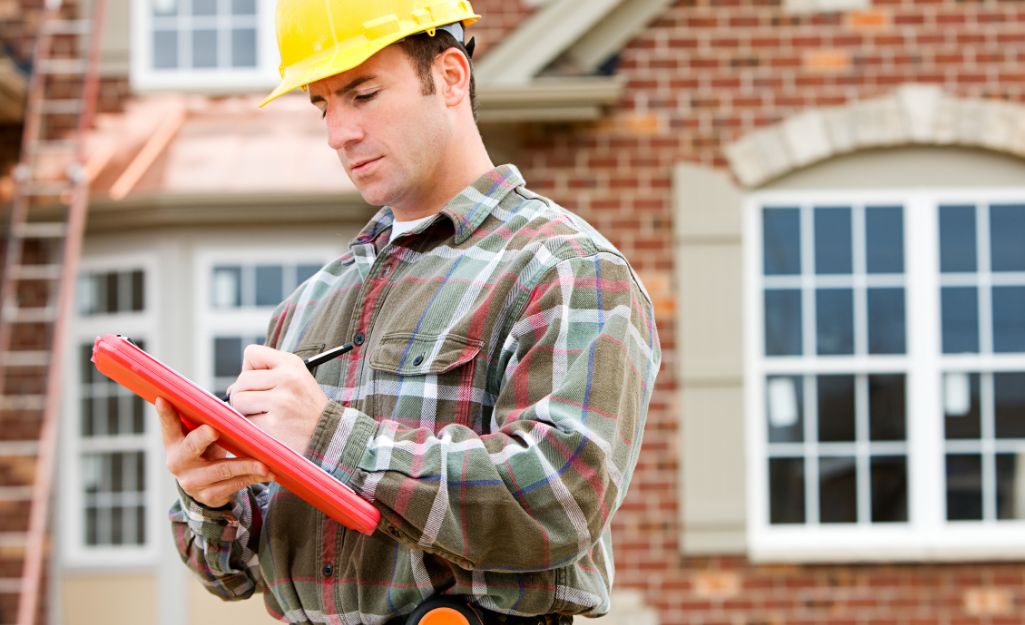
The process for construction bids typically follows these steps:
- The client solicits bidding on a construction project and provides relevant information such as blueprints.
- Pros perform any necessary due diligence to create an estimate, often visiting the site and asking relevant questions about the project’s scope or specifications.
- Pros create the bid by making as accurate an estimate as possible, which can include selecting subcontractors, calculating overhead and confirming the latest materials costs.
- Pros submit the bid before the set deadline.
- The client reviews the bids and selects the winner.
- The client and contractor confirm details and sign a contract.
The following are the basics of construction bids you should present to a potential customer.
- Company contact information
- Step-by-step description of the work
- List of required materials and labor
- Estimated timeline or completion date
- Total cost
- Payment terms, conditions and relevant guarantees
Pro Tip: Some Pros include with their bids testimonials from prior customers or awards they’ve received to convey a track record of success.
How to Estimate Materials Costs
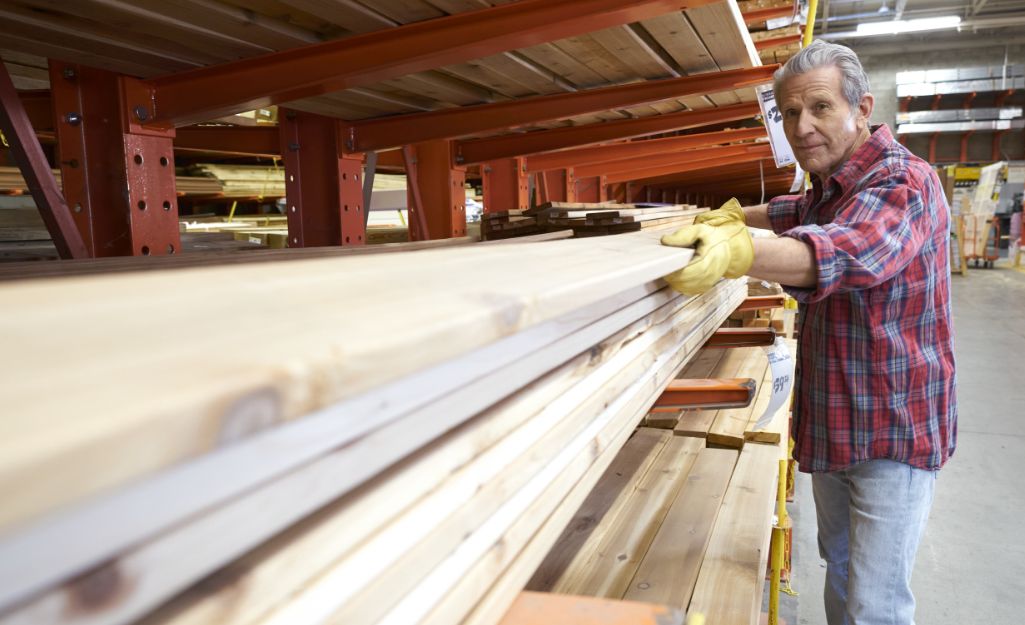
Making estimates for construction bids is vital for both the client and contractor. Accurate estimates allow customers to make the best decisions and ensure that contractors will make profits. The major areas of costs for construction estimates are materials and labor. In addition, include overhead or operating expenses when estimating the overall cost of a job.
For construction Pros, blueprints can be the best resource for estimating materials costs. (See our guide How to Read Blueprints.)
Using blueprints to estimate materials is sometimes known as the “quantity takeoff,” for “taking off” the necessary quantity of materials from the information in the blueprints. These are the steps for estimating the quantity of materials:
- Begin by determining type of building materials needed, such as the type of lumber or pipework. Different factors such as durability or sustainability may drive up the price, so discuss style preferences and budget limitations with the client.
- Use the dimensions of the project to determine the quantity of materials, such as the square footage of floors for the flooring.
- Multiply the quantity of materials by the local price. Be aware that materials can fluctuate in price over time, making the estimate out of date.
For a breakdown of the average materials costs of home exteriors and interiors, see our guide How Much Does it Cost to Build a House?
Pro Tip: Avoid price fluctuations in materials. Create a quote, prepare bids and lock in pricing using a free Pro Xtra account.
How to Estimate Labor Costs
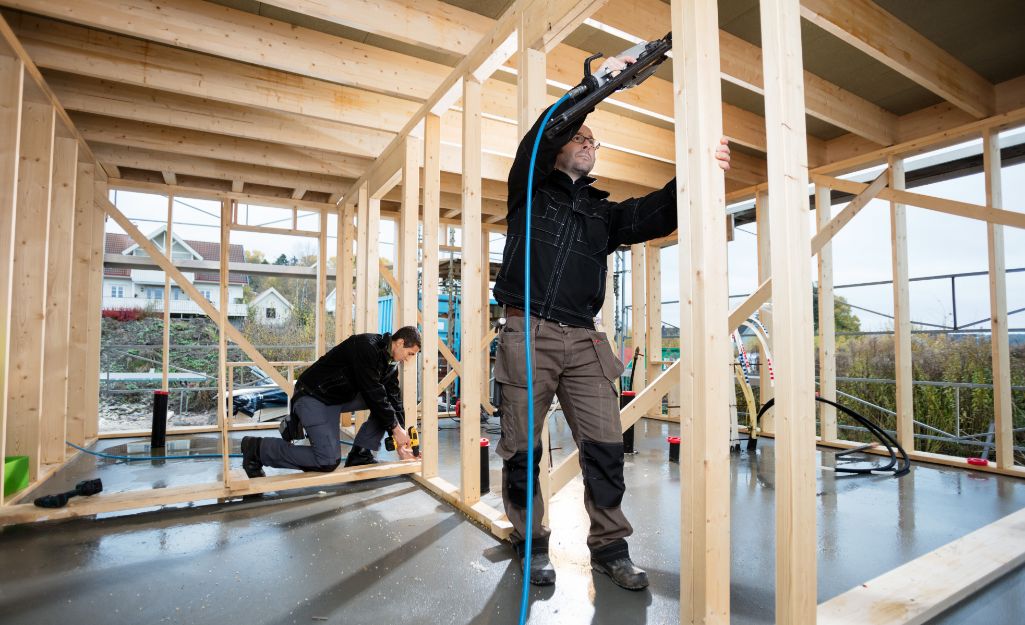
Labor costs are major factor for creating an estimate for construction bidding. Knowing your construction labor rate is essential for estimating labor costs.
- Begin by calculating the base rate for your crew. Add the hourly rates of the crew members to determine the base rate. Workers may have different specialties or experience levels, so they probably have different hourly rates. For example, if you have a crew of three workers who make $30, $25 and $25 an hour respectively, the base rate would be $80 an hour.
- Determine your labor burden, which includes worker-related expenses such as state and federal fees and insurance. For example, FICA is 7.65%, which would be $3.92, $3.26 and $3.26 per hour for the above workers, or $10.44 per hour.
- Add the labor burden to the base rate to determine your hourly construction labor rate. In the example above, the base rate plus FICA is $80 + $10.44 = $90.44. (This does not include state fees, insurance, etc.)
Use the construction labor rate in both the unit pricing method and the square footage method of estimating labor costs.
- In the unit pricing method, divide the project into individual jobs (or “units”), determine how long each job takes and multiply by the labor rate. For example, if building a wall takes 8 hours and the labor rate is $50, it will cost $400 to build the wall. Then add the units to make a total labor estimate.
- In the square footage method, determine the total square footage of the project and multiply that by the labor rate.
Overhead, also called fixed costs or operating expenses, includes costs to run your business, such as marketing, vehicle costs and office expenses. A National Association of Home Builders survey found that overhead is 10% of the annual budget of most building professionals. The bigger the business, the higher the overhead.
Pros should have an exact account of their operating expenses. For a rough estimate, add 10% to the materials and labor costs.
Finally, add your profit margin. Profit margins can vary from less than 10% to more than 30%.
Some Pros estimate total construction costs with a method called “The Rule of Two.” Conventional wisdom among some Pros holds that labor is up to 50% of costs. In a Rule of Two estimate, determine the labor cost of a job, multiply by 2 and add a 10% markup.
The Rule of Two method can be the quickest way to make an estimate, but also the most inaccurate. It can be useful to help you quickly identify jobs that may be too small or too big for your business.
Pro Tip: Most employees are not productive every minute of a day, with one study estimating that workers spend an average of 42 minutes per day not working. Some Pros may adjust for “time theft” in their labor cost estimates.
Tips for Construction Bidding
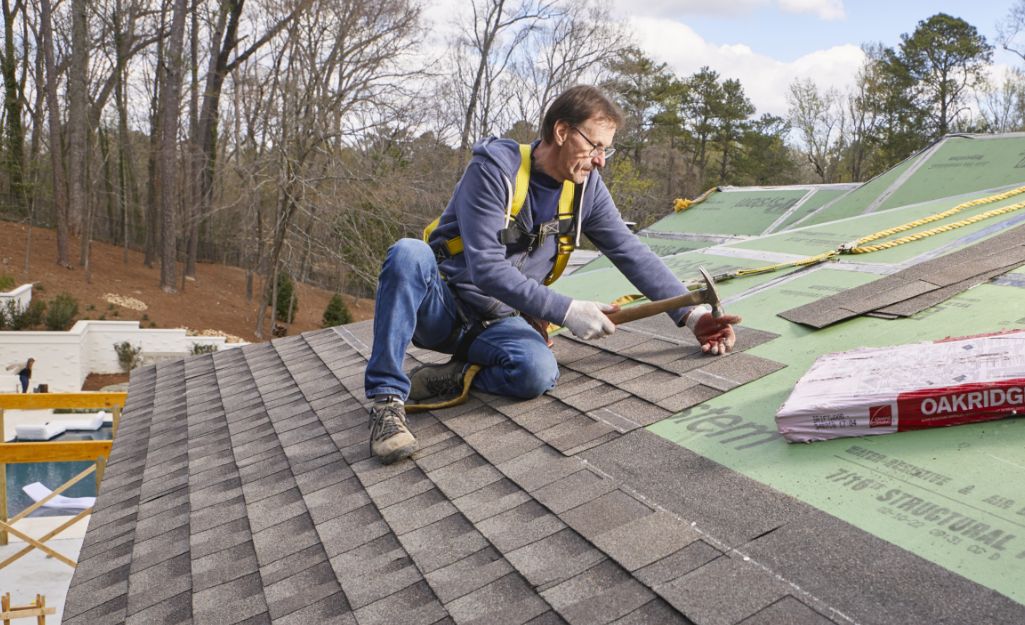
Consider the following tips for making construction bids.
- Cost estimation software can save time when making estimates for construction bids.
- Know the local market rate for your work. Keep up with how much your competitors charge for comparable projects.
- When working with subcontractors, confirm any quotes they provide you. Only work with reliable subcontractors.
- Consider risks and worst-case scenarios, such as delays or inflated materials costs. Make sure your estimate includes a cushion.
- Do not underbid or overpromise. If your work goes significantly over your estimate for time or cost, you may face a choice of either reducing your profit margin or annoying your client, which could cost you future business.
- When the job is over, review your bid to confirm that your estimates were accurate. If not, adjust future estimates accordingly.
More Tools. More Products. More Perks.
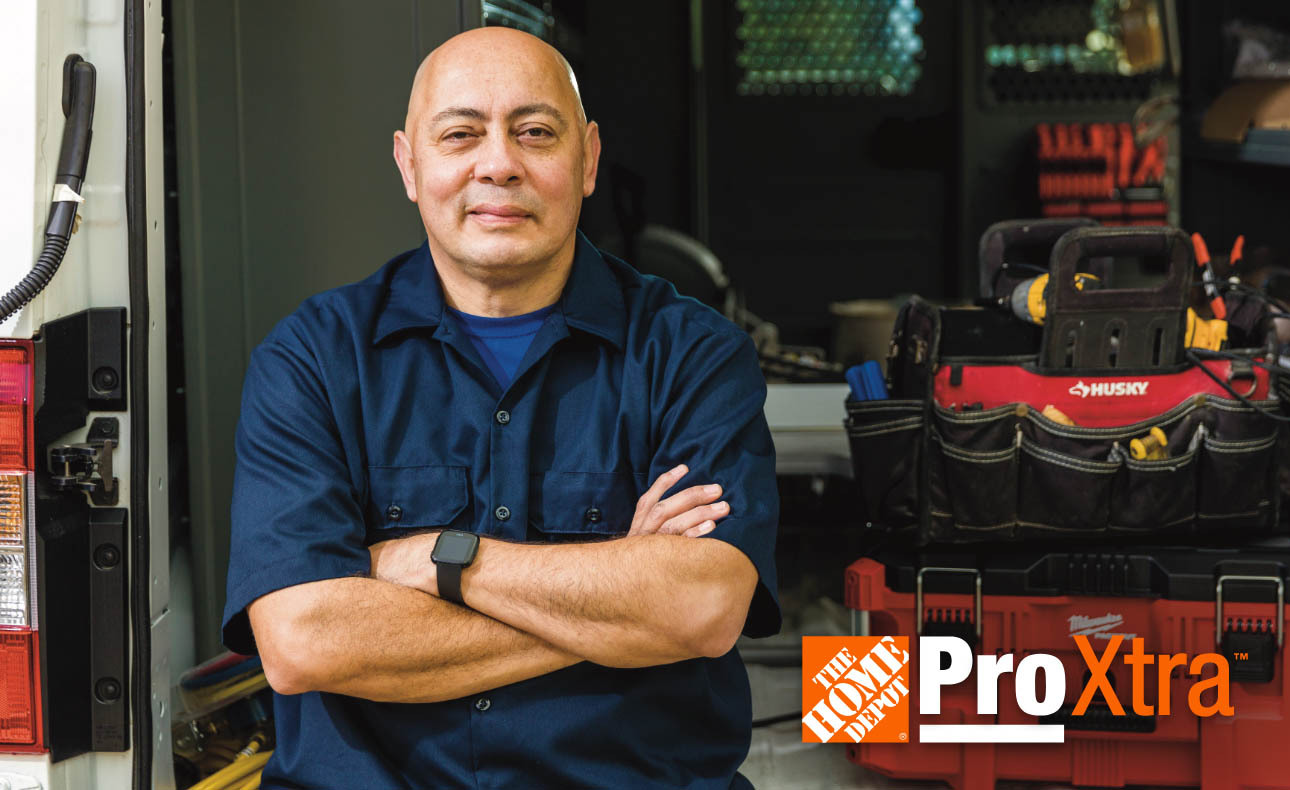
Be more competitive and boost your bottom line with Pro Xtra, The Home Depot’s free loyalty program built for Pros. Sign up today to access the enhanced Pro Online Experience, built with the online business tools and time-saving features Pros need.
Connect to local homeowners looking to hire pros like you with Pro Referral.