What Is Lean Construction?
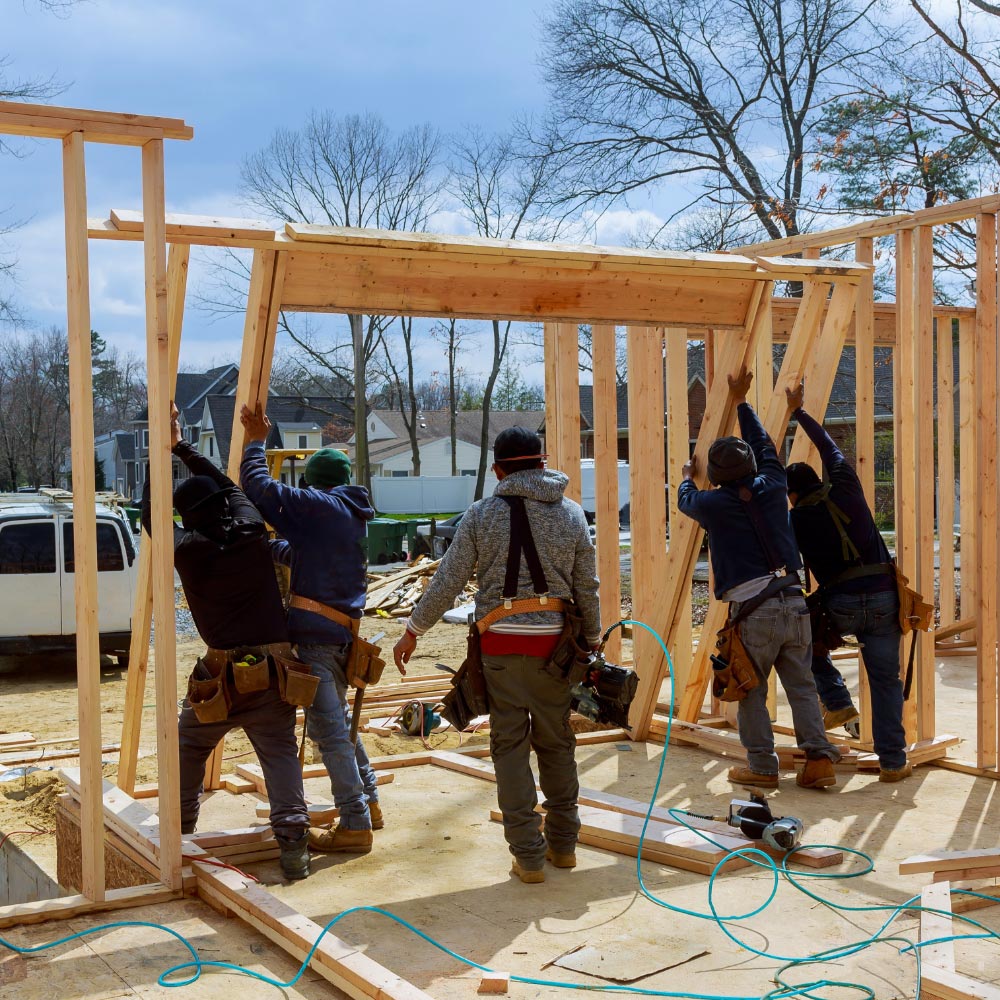
Last updated August 12, 2024
Lean construction refers to a set of principles and practices designed to create more efficient processes at the job site or workplace. Lean construction seeks to improve workflow, reduce waste and create more value for the customer.
This guide reviews the lean construction principles and cites examples of lean building jobs.
Table of Contents
What Are Lean Construction Principles?
What Are the Eight Types of Waste in Lean Construction?
What Are Examples of Lean Construction?
More Tools. More Products. More Perks.
What Are Lean Construction Principles?
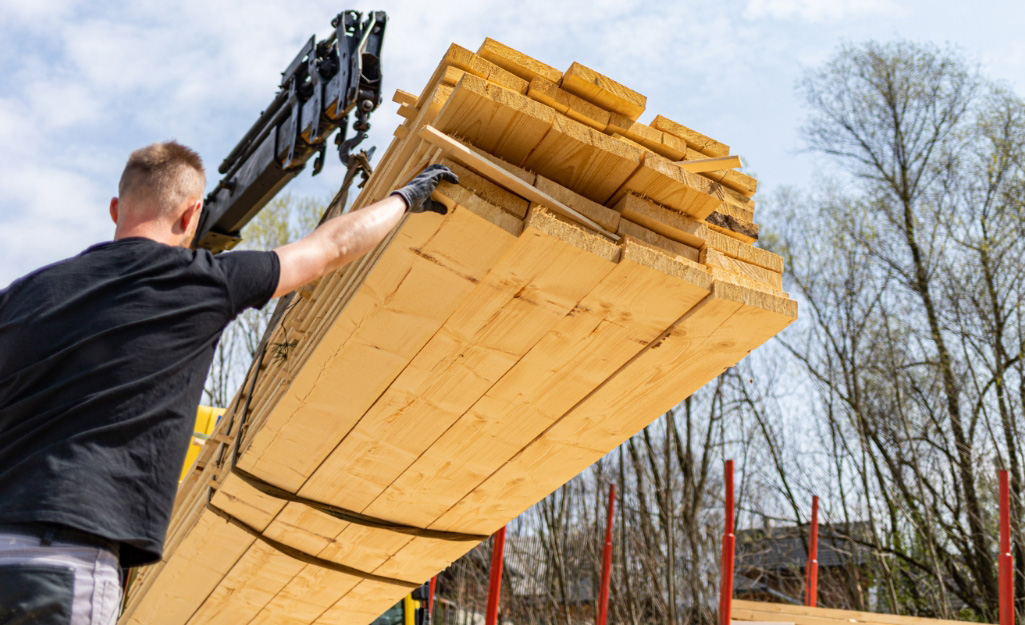
Lean construction is a project management approach that reduces waste, improves workflow and emphasizes collaboration between workers and teams in building jobs. It applies principles developed in manufacturing to increase efficiency in construction, including the supply chain, job scheduling, material inventory and other types of work.
Lean construction often refers to general principles rather than specific tasks. Groups that promote this approach include the Lean Construction Institute.
The first lean manufacturing principles began with Toyota Motor Corporation in the 1950s, which emphasized improving workflows and reducing waste. Lean manufacturing ideas were applied to construction in the early 1990s and have been used to find and develop best practices in construction ever since.
There are six general lean construction principles:
- Respect for people, including customers and team members
- Whole process optimization that encourages workers to focus not just on their individual jobs but the entirety
- Waste removal
- Focus on process and flow
- Value generation
- Continuous improvement
Often, lean construction includes identifying standardized procedures for clarity and consistency in performing tasks. This helps ensure that jobs are completed on time, on budget and to high standards. Lean construction values input from the workers who do the jobs and not just management.
In addition to fostering teamwork and transparency, lean construction often uses the following methods:
- Pull planning is a construction scheduling method that sets a “backwards timeline” beginning with the project completion date to set efficient deadlines.
- Integrated project delivery maximizes efficiency by gathering input from all stakeholders, such as design, fabrication and construction.
- Just in Time (JIT) delivery involves ordering and receiving items only when necessary to lower costs from inventory storage and waste.
- Last planner systems use detailed group planning and tight scheduling to create workflows that increase productivity and accountability.
Pro Tip: To control exactly when your supplies arrive at the job site, use our Scheduled Delivery option for online orders.
What Are the Eight Types of Waste in Lean Construction?
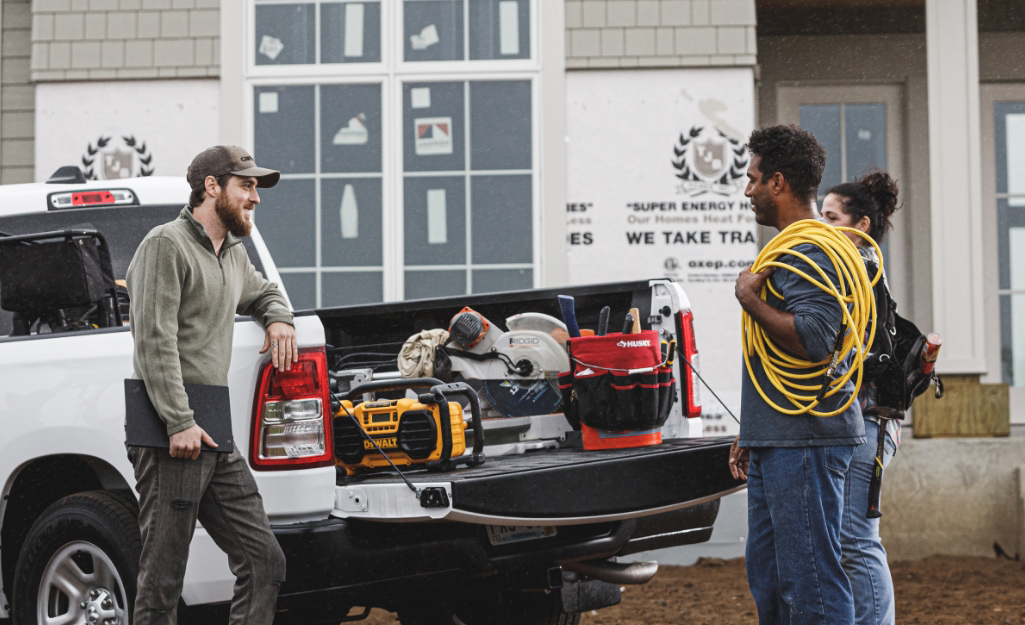
The goal of lean methodology is to reduce or eliminate wasted labor or materials in the construction process. Waste includes surplus materials in the supply chain, as well as any action that does not add value to the customer.
Lean Construction identifies seven types of waste, which together form the acronym “TIM WOOD:”
- Transport: Incurring unnecessary or excessive transportation costs for products, materials or equipment, such as bringing unnecessary tools to a job site or making too many stops during delivery.
- Inventory: Having excess tools or materials on site, which can involve unnecessary storage costs for raw materials or finished goods.
- Motion: Any unnecessary or inefficient movement of workers or equipment on site, including bending or reaching in ways that could cause injury.
- Waiting: Poor scheduling that leaves workers or equipment idle while awaiting deliveries or for the preceding jobs to finish.
- Overprocessing: Spending too much time or too many steps on a task. Overprocessing can include using high-precision equipment instead of a simpler, cheaper substitute when suitable.
- Overproduction: Creating more of a product than has been ordered or can be sold. This includes making the product before it has been ordered or is needed.
- Defects: Creating things that must be repaired or replaced, including work not installed to specifications.
In 1990s some experts added an eighth type of waste. “Skills” refers to underused abilities or talents of the workers. This addition changes the acronym to “TIM WOODS.”
Home construction has another way of categorizing types of waste:
- Required waste refers to stocking more items than necessary to replace ones that are faulty, break during construction, etc.
- Visible waste refers to surplus materials that must be hauled off, recycled or put into storage. Costs include both the materials themselves and the disposal or storage costs.
- Hidden waste refers to surplus or inefficiently used materials that cannot be seen when the job is over, such as drywall, sheathing or framing materials behind walls or under flooring.
Lean construction seeks to reduce all three types of waste with more detailed and effective planning and preparation, such as house framing plans that use materials more efficiently.
Pro Tip: The Associated General Contractors of America offers a Lean Construction Education Program online for Pros to lean more of the principles and techniques.
What Are Examples of Lean Construction?
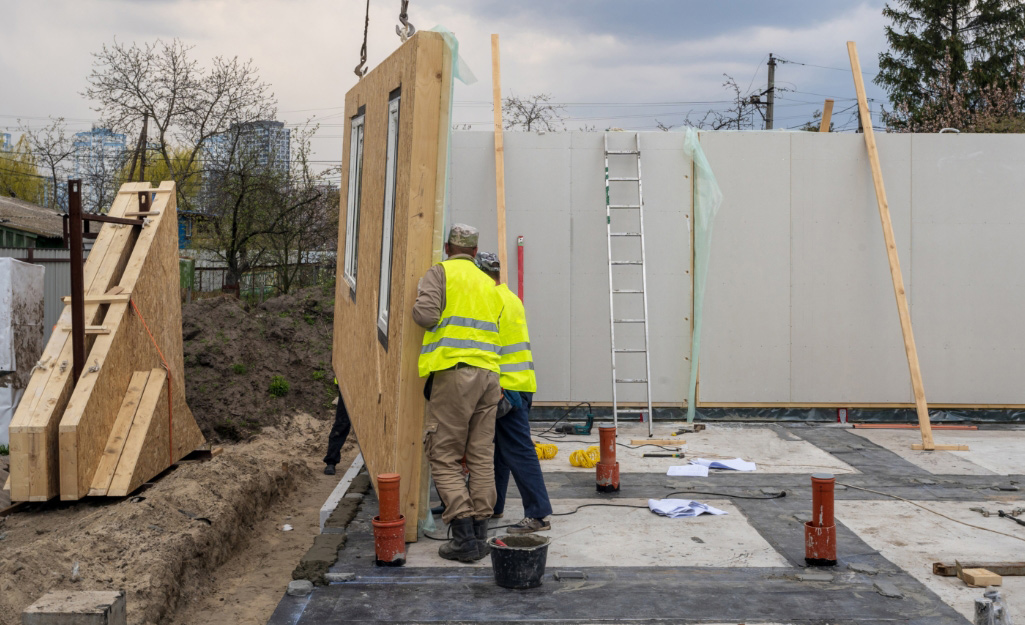
High-profile projects that used lean construction include The Shard skyscraper in London, The Children’s Hospital in Philadelphia and The University of California in San Francisco.
Off-site construction is an important lean construction method that involves manufacturing, fabricating or assembling items at a different location than the build site. These are the main types of off-site construction:
- Modular construction involves assembling 3-D units such as bathrooms at a factory and attaching them on site. These include frames made of lumber, composites, concrete or light gauge steel.
- Panelized construction is the assembly of flat panel units such as floors or walls.
- Hybrid construction uses both modular and panelized methods, such as a dwelling with modular kitchens built off site and assembled with panelized structures on site.
- Sub-assembly construction includes the off-site building of such components as roof trusses, staircases, beams and columns.
- 3-D construction printing (3DCP) uses 3-D printers to fabricate structural components off-site.
Lean construction software tools are developed to improve workflow and reduce costs. Examples of lean construction programs include virtual design, automatic scheduling and mobile inventory management.
More Tools. More Products. More Perks.
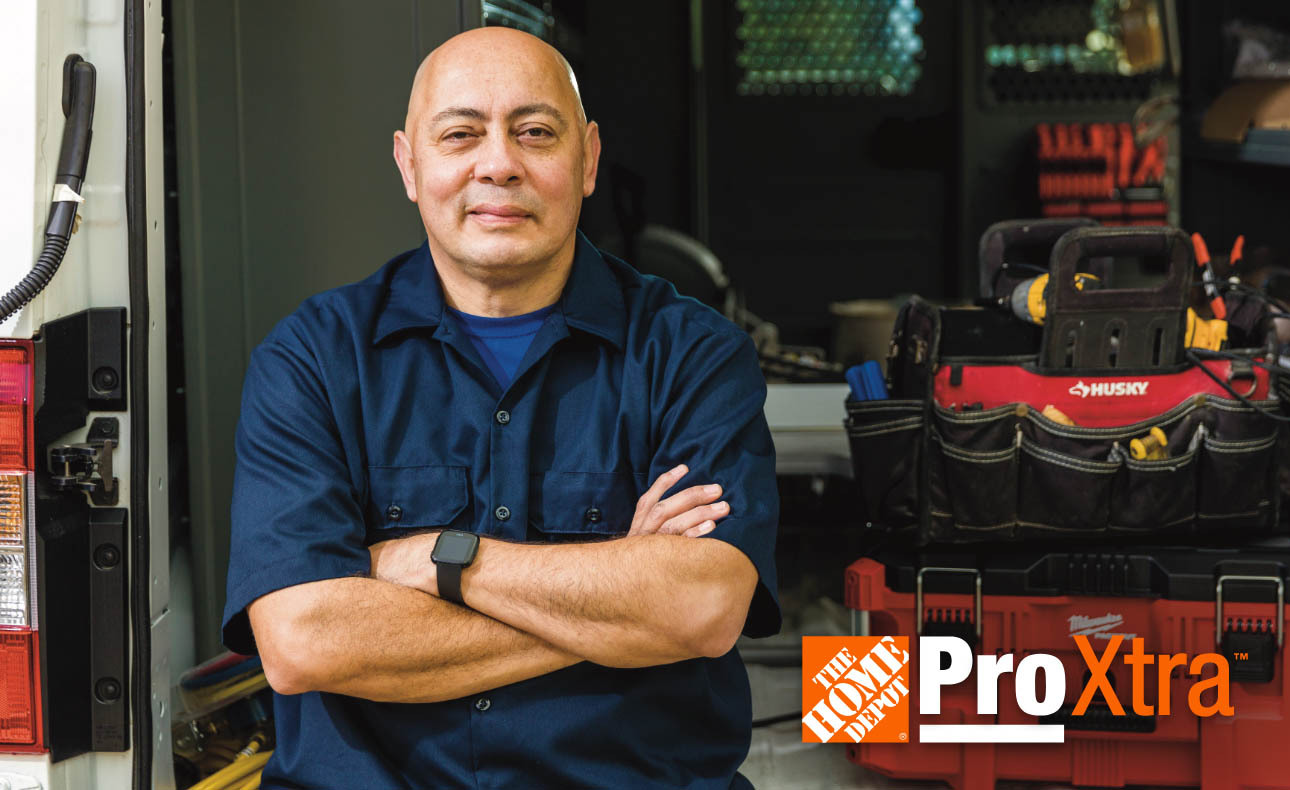
Be more competitive and boost your bottom line with Pro Xtra, The Home Depot’s free loyalty program built for Pros. Sign up today to access the enhanced Pro Online Experience, built with the online business tools and time-saving features Pros need.
Through the Path to Pro Network, you can post free job listings and find labor faster. Access a large pool of skilled candidates to keep your business running or help you find your next job opportunity in the trades.